Lost Wax Casting
Casting for filigree geometries
The proven rapid manufacturing technique lost-wax casting is the technology of choice for comparably fast productions of metal prototypes and small series of five to twenty pieces in a high-grade casting quality. DDV stands for the German term “Druck-Differenz-Vakuum” (differential pressure vacuum). At first the master pattern is duplicated in a lost-wax resin. The finished wax pattern, which is equipped with a feeder and vent tubes, is embedded into a special ceramic mass. Then it is melted out in a temper process, which takes several hours. The ceramic is burned until it reaches the required temperature stability. In the next step the metal alloy that has been fused inductively in a protective atmosphere beforehand, is cast into the casting mould. During the casting process the SPS control system facilitates a defined holding pressure on the metal melt. Even with filigree geometries good mould fillings and a reduction of cavitation shrink holes can be warranted using this process. After the casting and the curing process, the ceramic mould is destroyed by a jet of water and the cast part is demoulded.
Depending on the requirements, the cast parts are treated with jets or other adequate mechanical treatments, and thus are turned into the finished parts. This technique is especially inexpensive when the component part has a complex geometry and therefore its production would be too intricate or even impossible using other techniques such as CNC milling.
References Lost Wax Casting
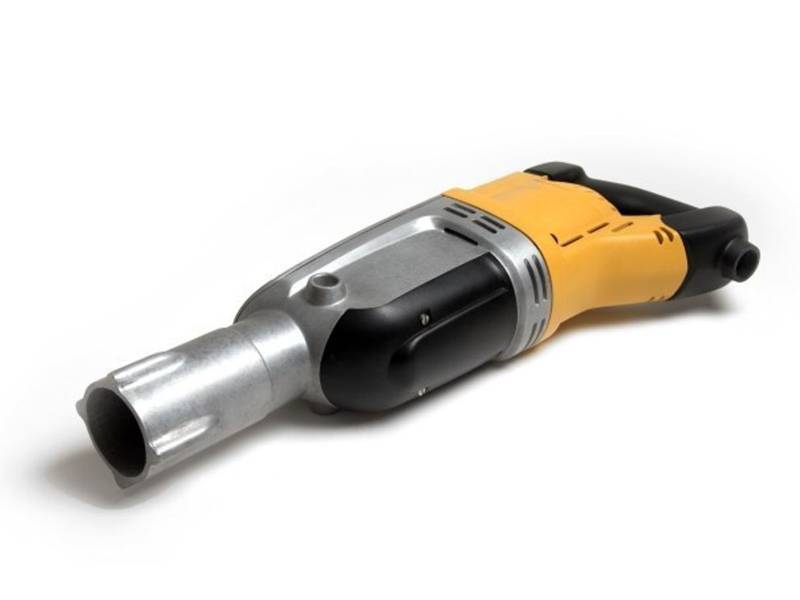
Hammer drill made of PU and lost wax castings
Functional prototype of a hammer drill produced by vacuum casting and investment casting.
> read more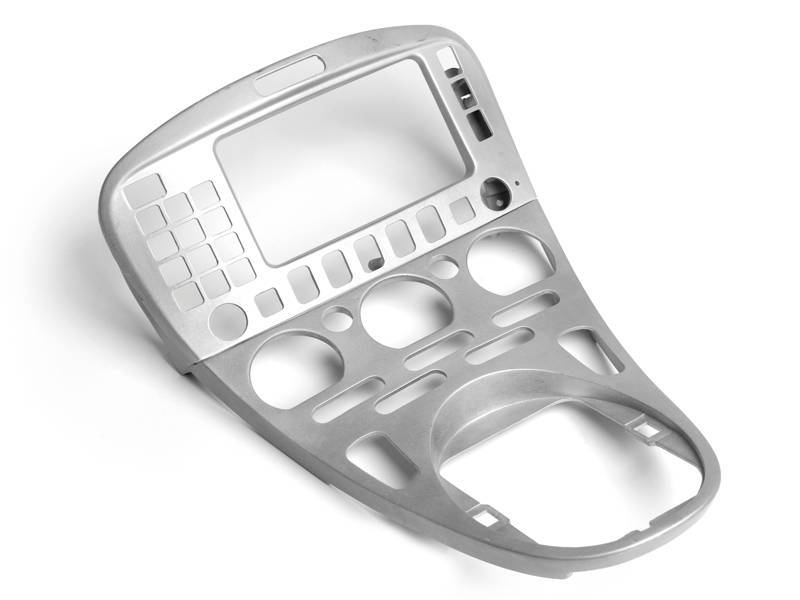
Center Console
Prototypes of center consoles manufactured via investment casting in aluminum.
> read more